市政污泥与煤配伍(磨制)焚烧特性试验
0 引 言
我国市政污泥产量随城镇化水平提高而不断上升,由于污泥内大量病原菌、多环芳烃、重金属等有害物质,其合理处置也愈发受重视。污泥处置方式大体包括填埋、土地利用、建材、焚烧等[1]。其中,焚烧因对污泥有害物质的无害化处置,减小污泥体积,成为最具发展前景的处置方式之一[2]。
燃煤耦合污泥发电作为焚烧处置的典型技术,具有处理量大、适应性强等特点,一定程度上解决了城市污泥处理难题。国家及地方相关主管部门相继出台了一系列相关鼓励政策,包括且不限于电价补贴[3-5]。
国内外学者针对污泥与煤混烧开展了广泛研究,苏胜等[6]利用热重法探究污泥及其与煤混烧的失重过程和燃烧特性,认为混烧特性在某些方面优于污泥与煤单烧,混烧方式可行。污泥燃煤耦合发电会对电站锅炉运行产生一定影响:吕清刚等[7-8]在CFB锅炉上开展混烧试验,污泥混烧率增加,炉内NO生成量增加,对N2O影响较小,适当提高炉膛温度,可降低N2O生成量,对NO生成量影响较小;降低污泥水分可提高燃烧效率,减少燃煤损耗;田甲蕊等[9]在CFB锅炉上掺烧印染污泥,结果表明,污泥质量比增加1%,炉温下降5.12 ℃,锅炉热效率降低0.78%,脱硫效率平均增加1.72%,烟气NOx减少1.93%,烟气中HCl增加3.33%,各排放指标均在合格范围,灰渣中重金属含量增加,建议掺烧比不超过20%;张成等[10]、朱天宇[11]、刘永付等[12]开展污泥与煤混烧的现场掺烧试验与数值模拟,结果表明,掺烧一定比例的污泥对煤粉锅炉正常运行影响较小,一定比例内混合燃料燃烧特性与煤的性质相近,大比例掺烧会导致入炉水分大幅增加,使炉膛温度降低,飞灰含碳量上升,燃料燃尽变差,NOx一定程度增加;狄万丰等[13]、魏林清[14]对掺烧污泥时机组运行参数进行优化,结果表明,燃煤电站掺烧污泥需严格控制污泥含水量(污泥比例),避免因入炉燃料水分过高导致磨煤机干燥出力不足、输煤系统堵塞、炉膛温度降低,影响机组安全稳定运行。
此外,城镇污泥中的毒害重金属,如Hg、As、Cd、Cr等,在掺烧过程中不易挥发的成分会聚集在大渣中排出,易挥发的成分会聚集在飞灰中或随烟气排出[15-16]。重金属元素分布在锅炉不同位置的灰渣中浓度不同。其中,Hg、As、He因其易挥发特性,燃用后以气态形式出现在烟气中,Pb、Cu、Cr、Ni沸点较高,更易留在大渣中, Cd沸点较低,大部分聚集在飞灰中,少部分在大渣中。与污泥相比,灰渣中的重金属元素并没有更强的浸出性和毒性,因此可进一步资源化利用[17-18]。
从实验室角度出发,分析不同污泥掺烧比例对原煤磨制特性、燃烧特性的影响,结合现场掺烧试验,更加系统全面地研究掺烧污泥对煤粉锅炉各系统的影响,为后续现场开展更高比例的污泥掺烧提供依据与参考。
1 研究方法
在磨煤机试验台上对掺烧污泥后混合样品磨制特性展开研究,在着火温度测试试验台上研究污泥掺入比例对着火特性的影响,基于一维火焰炉试验台分析掺入不同比例污泥对混合燃料燃尽特性、结渣特性的影响;随后在现场开展污泥掺烧验证试验,对燃煤电厂输煤系统、制粉系统、燃烧系统、汽水参数、锅炉效率、辅机运行、灰、渣与石膏的再利用、污染物生成等方面展开系统研究。
2 混合燃料燃烧特性
2.1 试验燃料
选取电厂常用劣质烟煤,与污泥掺混后进行相关试验研究。污泥来自污水处理厂,污泥样品全水为83.56%。磨制试验台为无干燥热源的试验钢球磨,污泥磨制前需进行晾晒处理,将干燥污泥与燃煤掺混后进行试验。
烟煤、干燥污泥的煤质指标见表1,所选燃煤为中等热值、中高挥发分、低灰分烟煤。干燥后污泥为中等灰分,高挥发分、低热值燃料[19]。干燥污泥掺入后,燃料中灰分升高、挥发分升高、硫分升高、热值降低。
表1 燃料的工业分析与元素分析
Table 1 Proximate and ultimate analysis of experimental materials

将燃煤与干燥污泥进行掺混,目前已掺烧污泥的电厂,掺烧比例通常不高于10%,考虑到试验代表性,试验样品中污泥占比分别设定为0、5%、10%、20%。
2.2 磨制特性试验
试验装置采用小型钢球磨,混样晾晒后放入磨中进行磨制。通过磨制相同时间后测试不同样品的煤粉细度(R200与R90),分析污泥掺入对煤样可磨性的影响。
混合样品磨制特性试验结果如图1和2所示,在钢球磨中磨制90 min,掺入污泥比例越高,煤粉细度越粗。
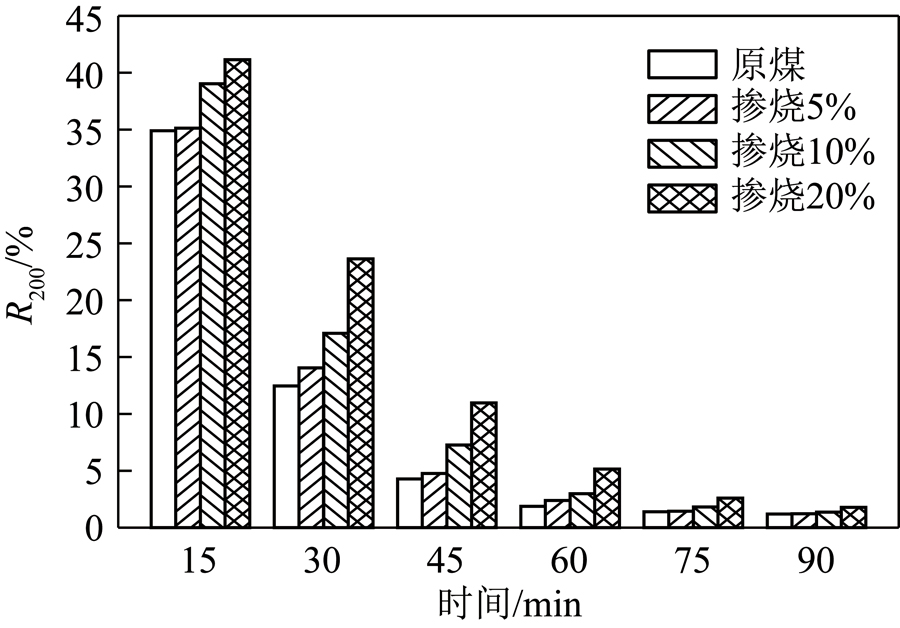
图1 掺配样品R200变化
Fig.1 Change of mixed sample R200
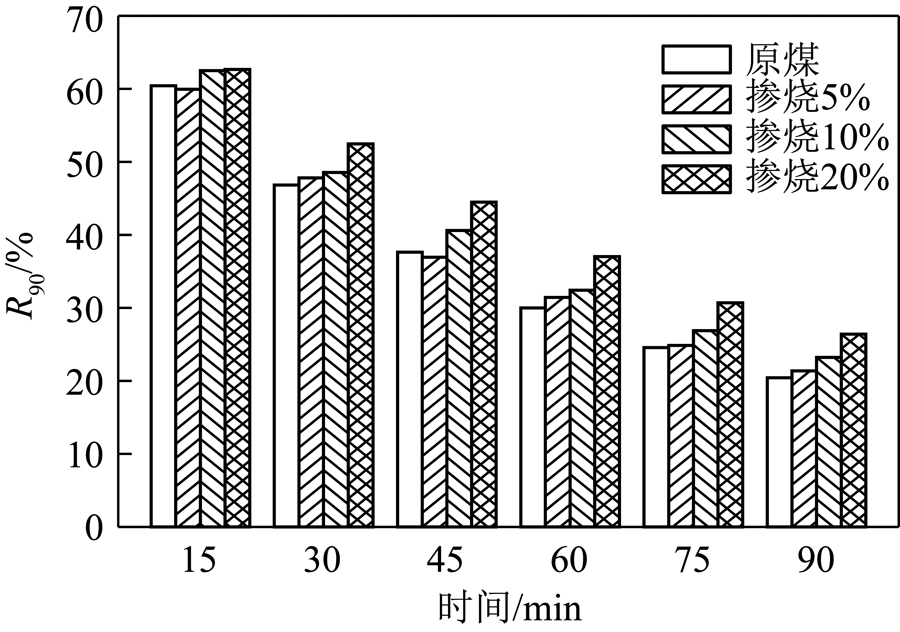
图2 掺配样品R90变化
Fig.2 Change of mixed sample R90
将掺入污泥后的样品继续研磨,磨至与原煤相近的细度,煤粉细度与均匀性见表2(n为煤粉均匀性指数),在磨制相近细度下,污泥掺入比例对煤粉均匀性影响较小。掺入比例越高,混合燃料可磨性降低,磨制相同细度燃料能耗增加。
表2 各比例下煤粉的细度与均匀性
Table 2 Fineness and uniformity of pulverized coal at various proportions
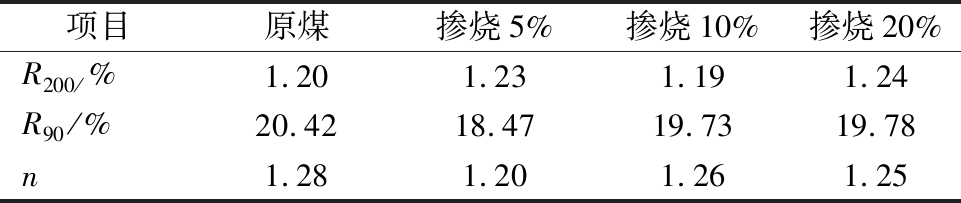
2.3 燃烧特性试验
燃料燃烧分为着火、燃烧和燃尽3个过程,着火、燃尽对燃煤机组锅炉安全和经济运行尤为重要,是新机组设计和已运行机组掺烧的重要参考依据[20]。
2.3.1 试验装置
利用着火温度测试试验台测试混合样品的着火温度,通过一维火焰炉试验台测试混样的燃尽率[21]与结渣特性[22]。
着火温度测试试验台如图3所示,包括炉体、送风机、引风机、给粉机、除尘器及控制系统组成,系统配有空气流量、压力、温度监测。
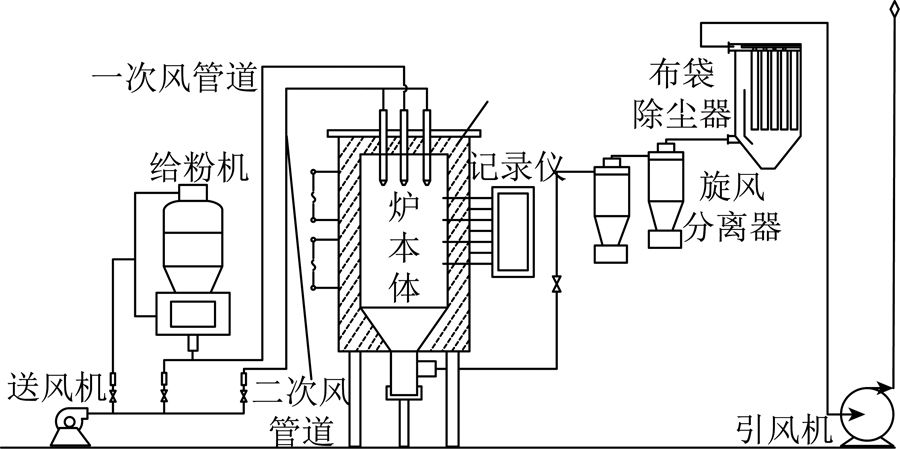
图3 着火温度测试炉及系统示意
Fig.3 Pulverized coal ignition temperature test furnace and system
一维火焰炉燃烧测试平台包括给料装置、送引风装置、炉本体、除尘器、控制系统等,如图4所示。
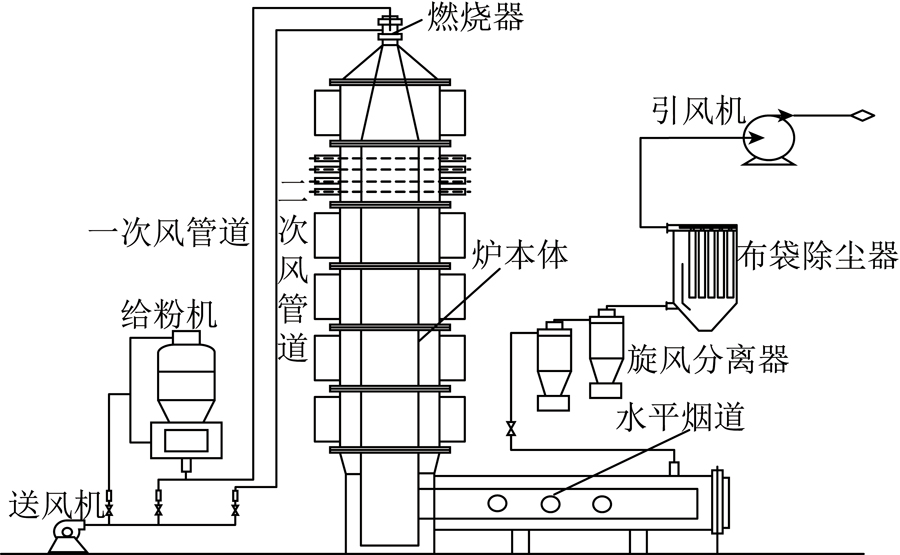
图4 TPRI煤粉燃烧一维火焰炉试验台
Fig.4 One-dimensional flame furnace combustion test bench of TPRI pulverized coal
2.3.2 试验条件
试验样品试验前为空干基状态,煤粉细度R90(%)按如下标准控制:

(1)
2.3.3 试验混样燃烧特性
根据测定的样品着火温度判断样品着火性能标准见表3。
表3 着火性能分级
Table 3 Classification of ignition performance

不同比例混样的着火温度如图5所示,原煤着火温度为460 ℃,属极易着火煤种。掺入污泥后,样品着火温度随污泥比例提高而升高,污泥比例5%、10%、20%、100%样品着火温度分别为483、494、496、518 ℃。
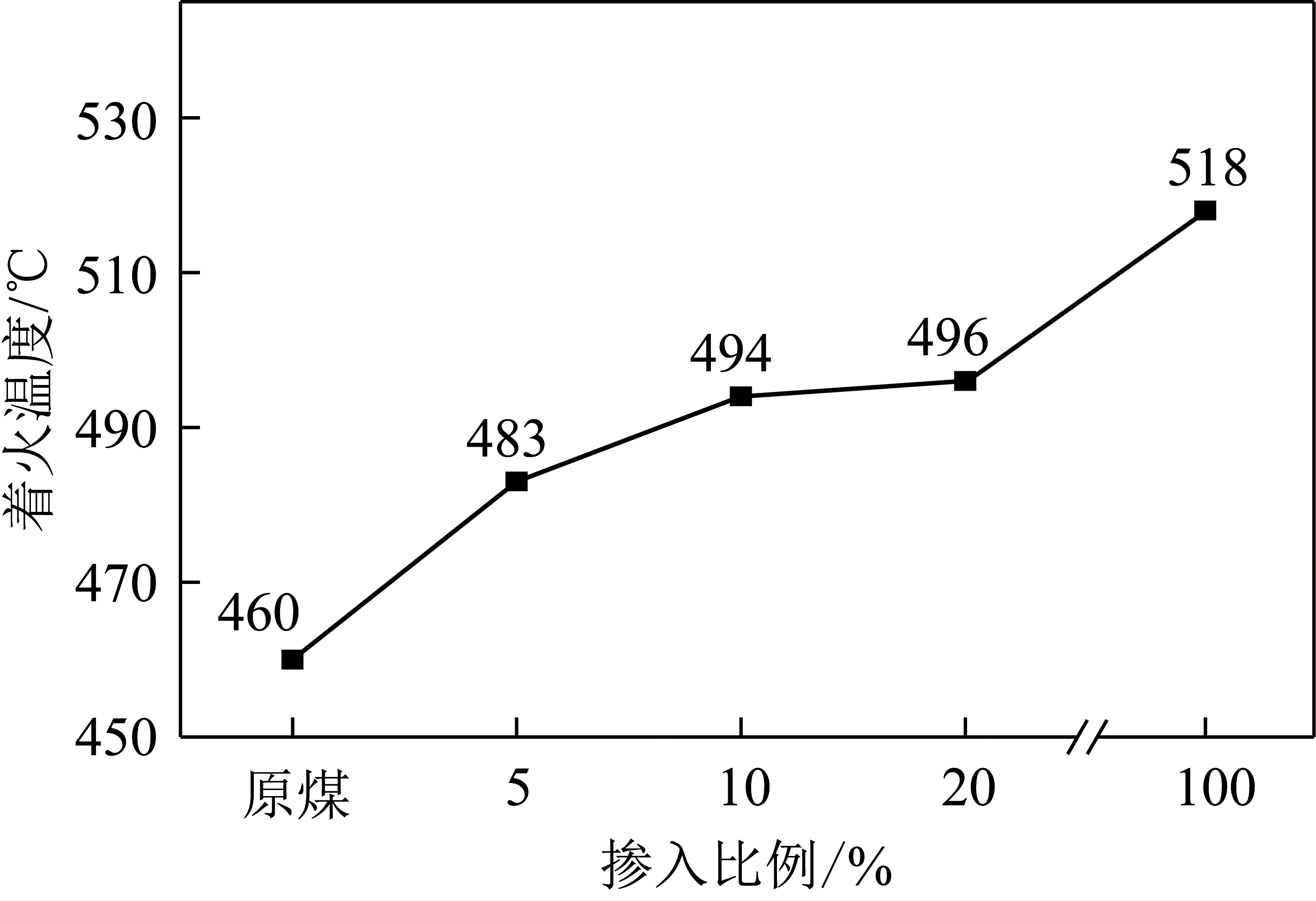
图5 掺配样品着火温度变化
Fig.5 Ignition temperature change of mixed sample
向燃料中掺入污泥,污泥的高灰分对燃料着火具有阻燃作用,使燃料着火温度升高、着火特性变差。
2.3.4 试验混样燃尽特性
在一维火焰炉上测定煤种的燃尽性能,燃尽性能的计算、评价方法见GB/T 39833—2021《煤的燃烧特性测定方法 一维炉法》。
一维火焰炉测试燃尽率结果见表4,原煤燃尽率为99.35%,属极易燃尽煤种,掺入污泥后,混合燃料燃尽率呈下降趋势。掺入20%的污泥,混合燃料燃尽等级由极易变为易。
表4 样品燃尽率
Table 4 Mixed sample burnout rate
掺入干燥污泥,混合燃料挥发分较原煤略有提升,挥发分的提升有助于燃料燃尽率的提高。但掺入高灰分污泥,灰分在燃烧初期对燃煤剧烈燃烧具有减速降温作用,大比例掺烧污泥一定程度上会降低燃料燃尽率。
2.3.5 试验混样结渣特性测试
试验采用一维炉结渣工况,结渣性能的计算、评价方法见DL/T 1106—2009《煤粉燃烧结渣特性和燃尽率一维火焰炉测试方法》[23]。
为区分探针表面结渣程度,测试其表面附着灰渣黏结紧密程度,从强到弱分为熔融、黏熔、强黏聚、黏聚、弱黏聚、微黏聚与附着灰7个形态。根据煤粉结渣特性评价指标Sc对试验煤种进行结渣性能判别,Sc判别评价指标见表5,计算公式如式(3)、(4)。
表5 一维炉判定煤粉结渣特性分级
Table 5 Determining the classification of pulverized coal slagging characteristics on one-dimensional furnace


(3)

(4)
式中,Nmax 为结渣最重渣型赋值,Tmax为结渣最严重等级渣棒对应的烟温,如果等级相同,取最低温度;T2为结渣次高等级渣棒对应烟温,如果等级相同,取最较高温度。
当结渣最严重与次严重的渣型相差1个等级时,采用式(3),当结渣等级相差2个及以上等级时,计算采用式(4)。其中N取值见表6。
表6 N取值
Table 6 N values
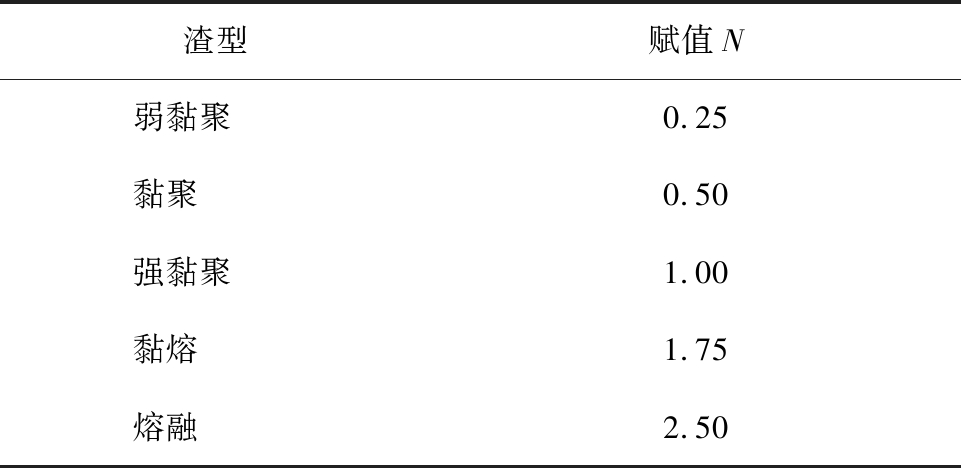
图6为各煤种渣棒表面结渣形态对比,渣棒从左到右对应炉膛的顶部到底部测点。各样品在1 200 ℃左右均出现熔融渣型,试验时的烟温与渣型、各煤种结渣指数Sc见表7。

图6 掺配样品结渣探针
Fig.6 Slagging probe of mixed sample
表7 样品结渣温度与渣型
Table 7 Slagging temperature and slag type of sample
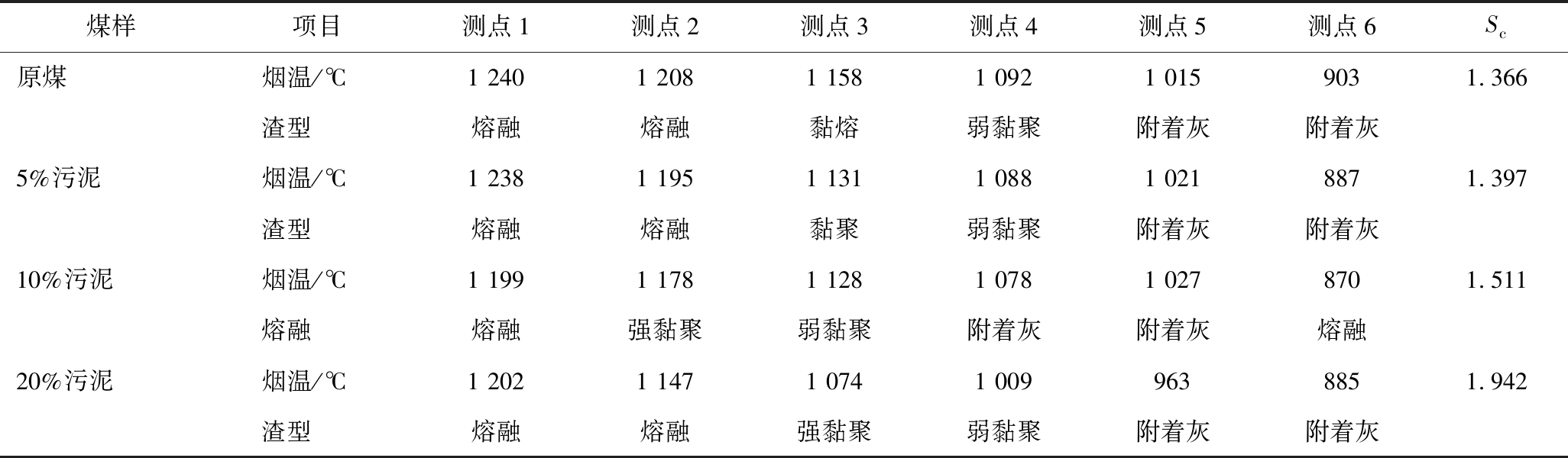
根据Sc结渣判别标准,以上4种煤结渣指标Sc均大于0.65,属于严重结渣倾向。掺入污泥会加重燃料结渣倾向,掺入比例越高,混合燃料结渣倾向越严重。
与纯煤相比,随污泥比例提高,混合燃料的灰分升高,沉积到结渣探针表面的灰渣量增加,飞灰浓度升高,结渣倾向加重,掺烧污泥时需关注高比例掺烧带来的结渣问题。
3 现场试验
3.1 试验燃料
在江阴某电厂锅炉(SG-420/13.7-M417A超高压自然循环汽包锅炉)上开展了污泥掺烧试验。外供污泥经过简单脱水处理后入厂,水分在40%,目前电厂缺少干化设备,故以直掺方式进行试验。
掺配试验时维持锅炉蒸发量不变,掺烧比例从6%开始,对系统各部分设备适应性进行评估,如对正常运行有较大影响,立即停止试验;设备适应性良好则加大污泥掺烧量。试验过程中掺烧量增至10%,基于生产安全考虑以及10%掺烧量已完全满足现阶段污泥处理量要求,故不再进一步增加比例。
现场掺烧试验条件下,不同污泥掺烧比例下的入炉煤质见表8。可知随污泥比例增大,水分、灰分、挥发分、全硫均升高,热值下降。热值变化导致入炉煤量变化,掺烧10%污泥,煤量增加8.46%。
表8 不同污泥掺烧比例下入炉煤煤质指标
Table 8 Coal quality index of coal fed into boiler under different sludge blending ratios

3.2 对输煤系统的影响
拟掺烧污泥全水40%,为颗粒状,可直接在煤场或上煤过程中掺混。不同污泥掺烧比例下给煤机输送带输煤状态如图7所示。在试验污泥掺烧比例条件下,输煤带上煤流均呈松散状态,未出现煤流黏聚成团或水分过大引起的输送不畅现象,整个输煤带、煤仓、落煤管、给煤机等均未出现堵塞现象。
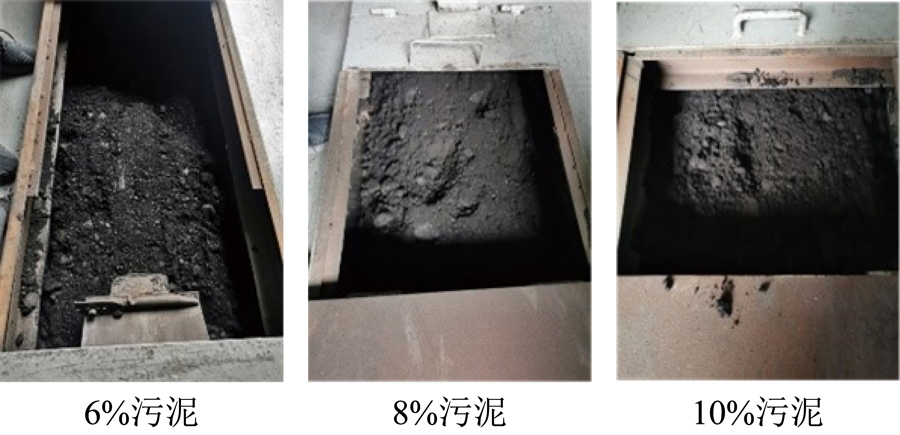
图7 掺入污泥后给煤机输送带状态
Fig.7 Status of coal feeder belt after adding sludge
3.3 对制粉系统的影响
在现场掺烧试验中,制粉系统采用抽炉烟混合干燥方案,其主要运行参数见表9(甲、乙为锅炉风机设备编号)。在试验范围内,随污泥掺烧比例提高,入磨燃料水分增加,为维持磨煤机出口温度在安全范围并留有一定余量,磨煤机进口风温逐渐上升,磨煤机出口风温、电流、压差、粉仓温度等都在正常水平。综合来看,试验范围内制粉系统能够正常运行。
表9 制粉系统运行参数
Table 9 Operating parameters of pulverizing system
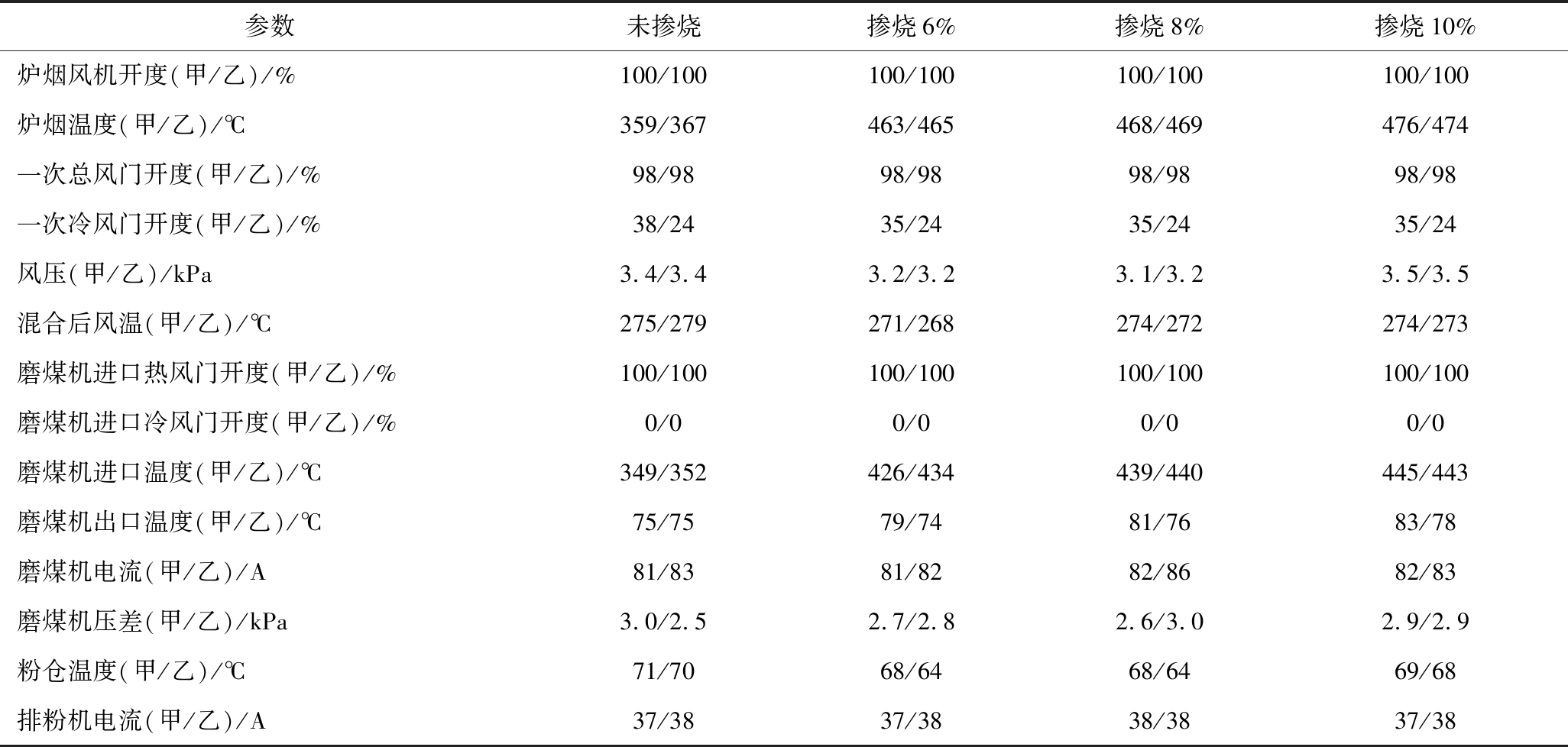
锅炉制粉系统对掺烧6%、8%和10%比例的污泥整体上适应。污泥掺烧对制粉系统的主要影响在于以下2方面:① 污泥水分偏高影响制粉系统干燥出力;② 污泥热值低造成入炉燃料总量增加影响制粉系统研磨出力。
3.4 对锅炉效率的影响
现场掺烧试验见表10。 现场掺烧试验表明,掺烧6%、8%和10%污泥,修正后的锅炉效率分别提高0.56%、0.73%、0.58%。说明污泥掺烧比例小于10%,对锅炉燃烧效率影响较小,试验过程中并未出现影响锅炉燃烧稳定性的情况。
表10 锅炉主要运行指标
Table 10 Main boiler operation index
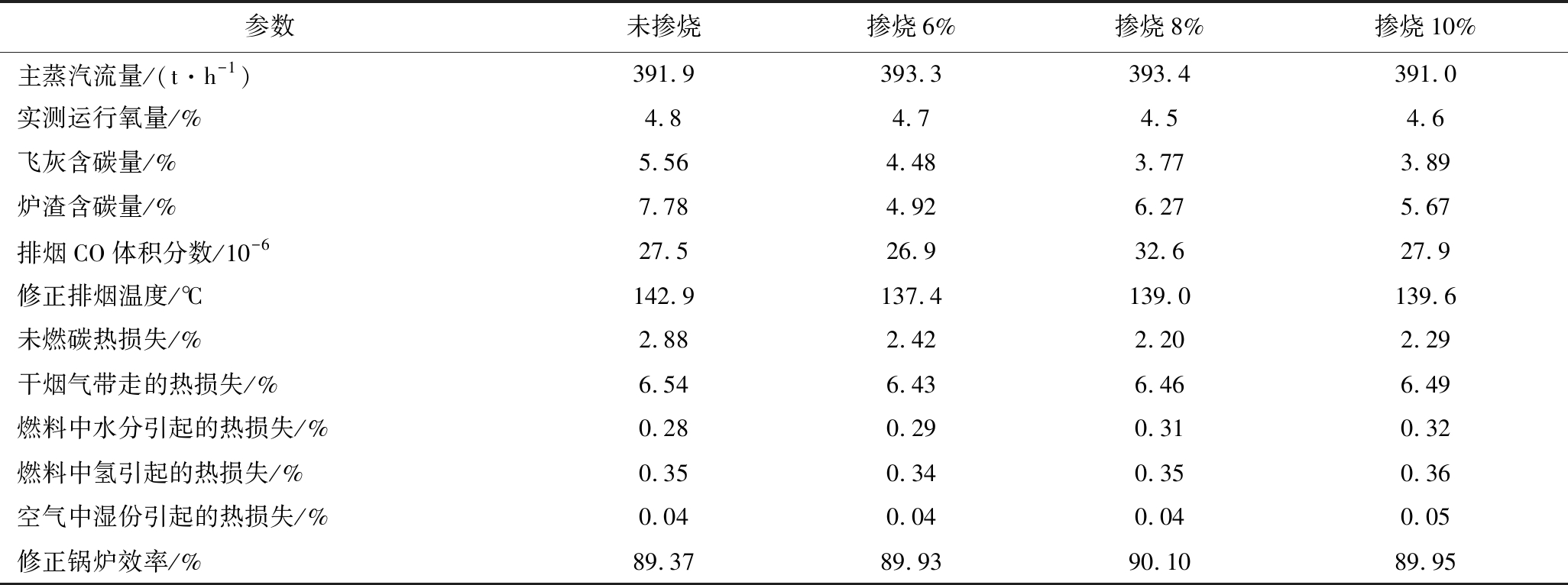
3.5 对汽水参数的影响
不同掺烧比例下的锅炉汽水参数见表11。锅炉主、再热蒸汽参数均可达正常值,过热器、再热器减温水量(开度)随污泥掺烧比例的提高而增加,主要原因是由于污泥热值低,掺烧后燃料量增加,烟气量增加,使对流换热增强。
表11 汽水系统参数
Table 11 Steam-water system parameters
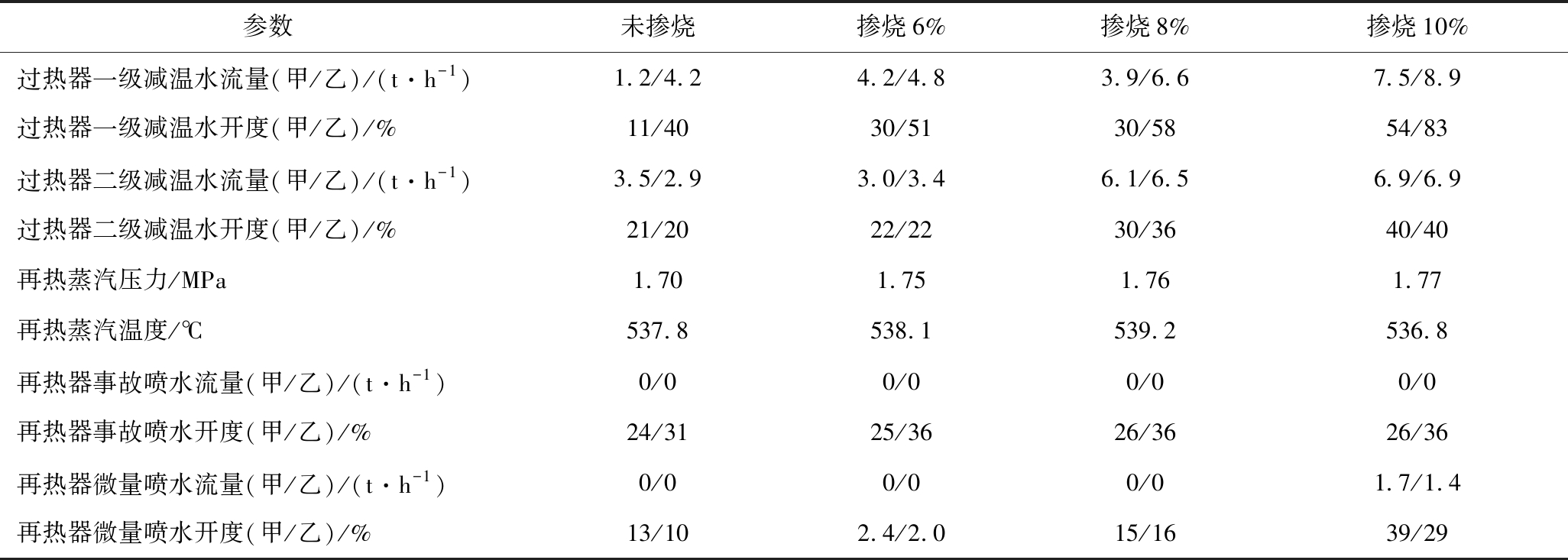
3.6 对燃烧和结渣的影响
不同污泥掺烧比例下的炉膛温度如图8所示。炉内高温区主要集中在燃烧器区域,该位置也最易结渣。由于污泥热值较燃煤偏低,因此掺烧污泥后炉内燃烧强度下降,与空白试验相比,掺烧污泥后炉膛不同标高温度均有所降低。与空白试验相比,掺烧10%污泥的最大温度降低约60 ℃。
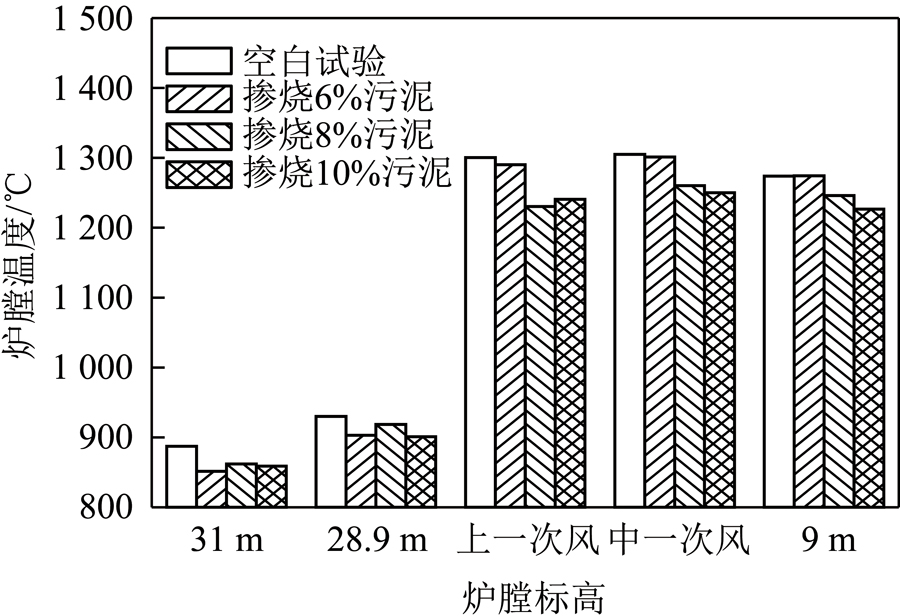
图8 炉膛温度随掺烧比例的变化
Fig.8 Change of furnace temperature with the proportion of mixed combustion
3种污泥掺烧比例下的屏区状况如图9所示。可见在3种掺烧比例下,屏区管子均清晰可见,干净无渣。燃烧器区水冷壁状况无法肉眼观测,但从炉膛温度测试结果分析,未出现明显的结渣加剧。综合分析,掺烧10%以内的污泥,对炉内燃烧基本无影响,不会引起炉内结渣加重等情况。
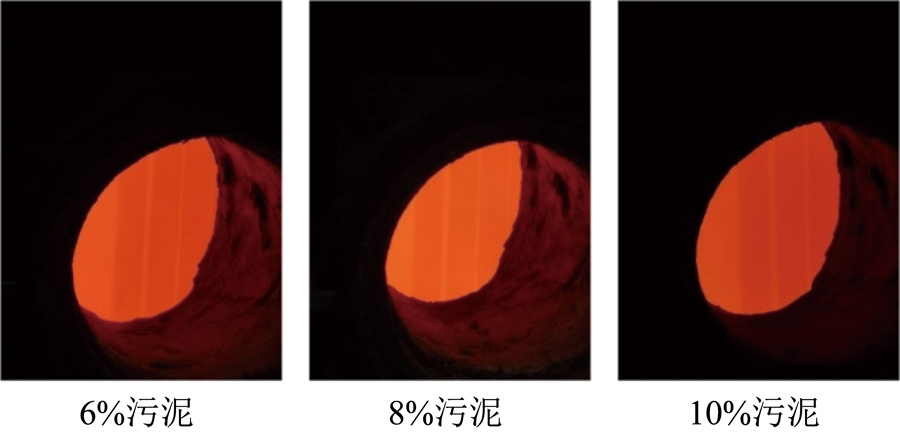
图9 28.9 m标高屏区结渣情况
Fig.9 Slagging in 28.9 m elevation screen area
从灰分角度来看,在实验室掺入20%干污泥,相当于40%水分的污泥掺烧比例达到30%,掺入比例较高,实验室结果变化较明显。同时,由于水分的影响,现场燃用过程中炉温降低,掺入10%的污泥,未观察到明显的结渣加重现象。
3.7 对锅炉辅机运行的影响
分别掺烧6%、8%、10%污泥后,计算得到总烟气量分别变化0.996%、-2.500%、-2.100%,掺烧10%左右比例污泥对一次风机、送风机、引风机基本无影响,一次风机、送风机、引风机基本不需要考虑污泥掺烧带来的影响。
污泥直接送入锅炉燃烧,污泥中的有毒有害物质在高温条件下基本完全分解,燃烧后的烟气中H2S和NH3浓度非常小,不会对送风机的叶片造成腐蚀。因此不会对送风机叶片安全运行造成威胁,但需加强对送风机叶片的定期检查工作。
3.8 对飞灰、大渣、石膏的影响
分别取掺烧6%、8%、10%污泥后的飞灰、大渣、石膏样品进行检测,飞灰、大渣、脱硫石膏中检测的氰根离子及烷基汞结果见表12,银、钡、铍、镉、铬、镍、铅、铜、锌、六价铬、硒、砷、汞、氟离子等的检测结果见表13。
表12 飞灰、大渣、石膏中氰根离子及烷基汞含量
Table 12 Content of cyanide ion and alkyl mercury in fly ash, slag and gypsum
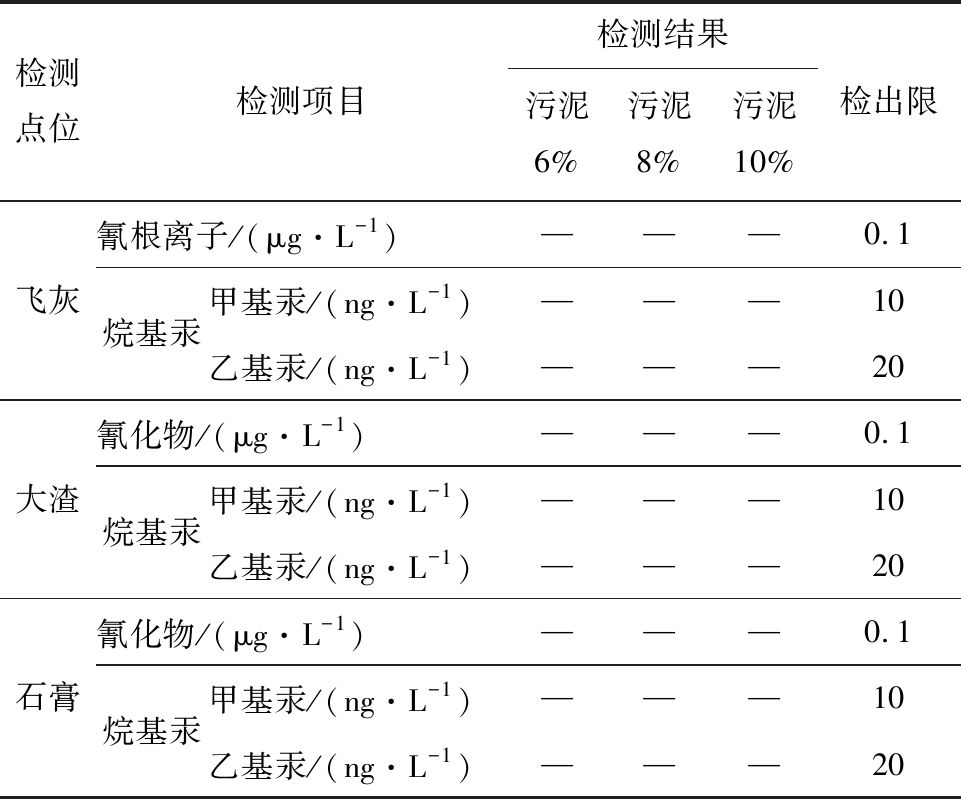
表13 飞灰、大渣、石膏浸出毒性检测结果
Table 13 Toxicity test results in fly ash, slag and gypsum
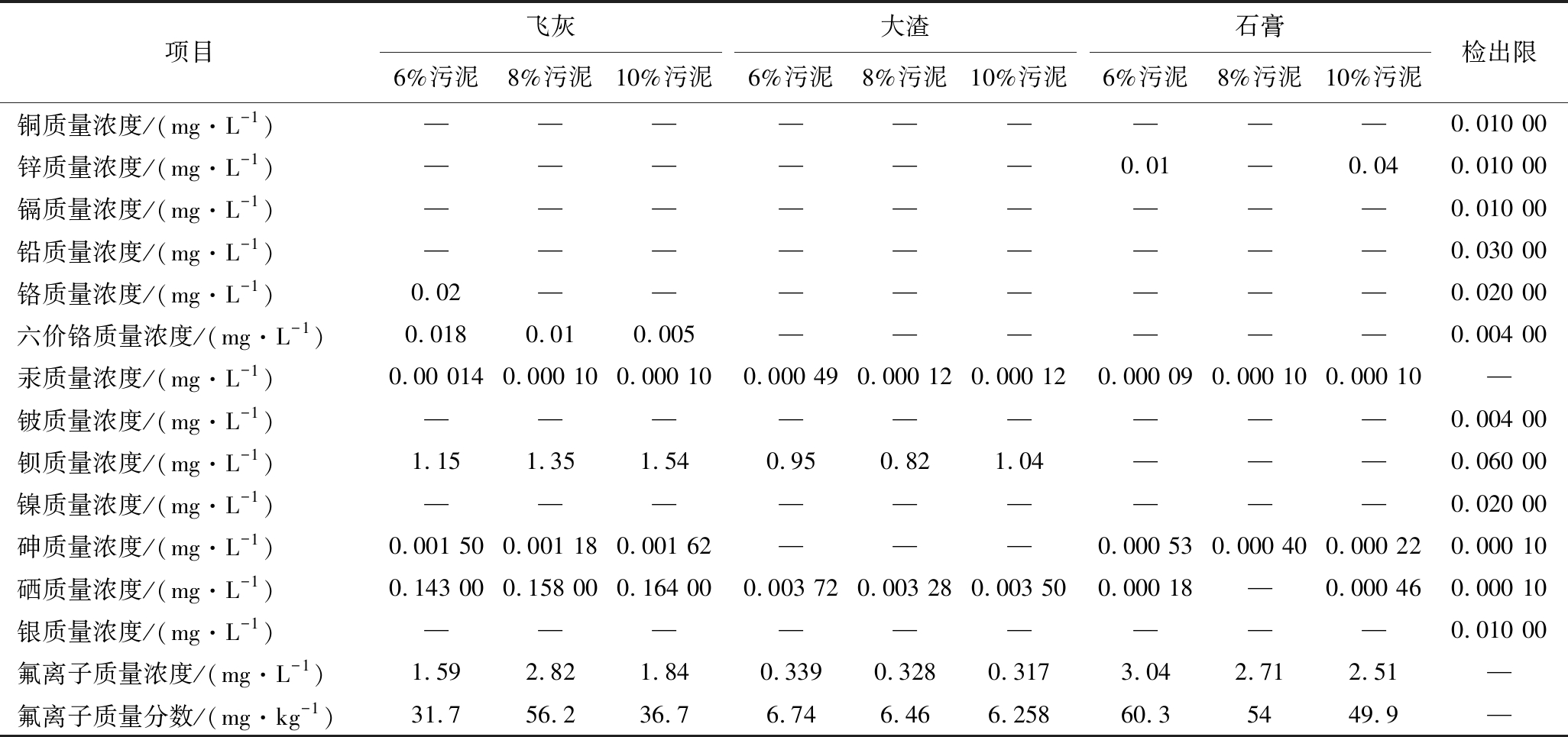
飞灰、大渣、石膏中所含固废及危废含量都在排放限值以内,满足国家标准要求。因此,本项目掺烧10%左右比例的污泥不会影响飞灰、大渣和石膏的品质和利用。
3.9 对锅炉污染物生成的影响
污泥掺烧对污染物生成的影响,在现场掺烧试验中,分别取掺烧6%、8%、10%比例污泥前后的污染物排放进行检测,见表14。
表14 污染物排放指标
Table 14 Indicators of pollutant emission
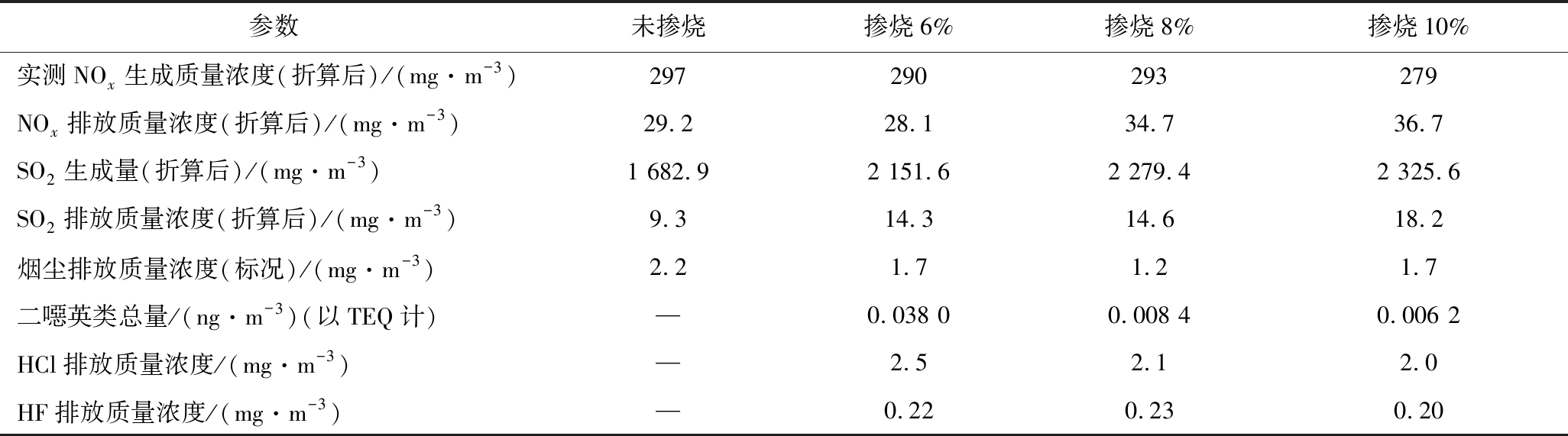
与掺烧前相比,锅炉掺烧6%、8%、10%比例污泥后的情况为:
1)脱硝入口NOx生成浓度基本无变化、甚至略有降低。
2)脱硫入口SO2生成浓度随着污泥掺烧比例的增加逐渐升高。
3)烟气中的二噁英毒性当量最高为0.038 ng/m3(11% O2,以TEQ计),远低于GB18484—2001《危险废物焚烧污染控制标准》规定的0.5 ng/m3 (11% O2,以TEQ计)以及GB 18485—2014《生活垃圾焚烧污染控制标准》中规定的0.1 ng/m3 (11% O2,以TEQ计)二噁英排放标准。
4)烟气中HCL、HF最高值为2.5、0.23 mg/m3,均远低于GB 18484—2001《危险废物焚烧污染控制标准》以及GB 18485—2014《生活垃圾焚烧污染控制标准》中规定的排放标准。
5)从排放浓度看,烟尘≤10 mg/m3,SO2≤35 mg/m3,NOx≤50 mg/m3,可达到《煤电节能减排升级与改造行动计划(2014—2020年)》中规定的超低排放标准要求。二噁英、HCl、HF排放浓度要求也都在相关国家标准规定的限值以内。
因此,在试验范围内,掺烧污泥后烟气NOx、SO2、烟尘、二噁英、HCl、HF排放浓度均满足国家标准要求。
4 结 论
1)向原煤中掺入干污泥,掺入比例越高,入炉燃料可磨性越低。现场掺入比例10%及以下污泥,制粉系统受到影响较小。
2)随干污泥掺入比例提高燃料着火温度升高,燃尽率下降,掺入20%干污泥,燃料燃尽率下降1.5%;随掺烧比例提高,燃料结渣倾向加重。现场掺烧试验,掺入10%及以下污泥,炉内燃烧稳定,炉温降低,对于燃料燃烧性能影响较小,未出现严重的炉内结渣情况。
3)污泥现场掺烧试验,掺烧比例10%及以下时,机组的输煤系统、制粉系统能够正常安全稳定运行,对锅炉运行效率整体影响不大,不影响锅炉燃烧稳定性,锅炉的汽水参数正常,辅机运行正常;飞灰、大渣和石膏的重金属浸出毒性检测均远低于排放限值,污泥的掺烧不会影响飞灰、大渣和石膏的品质和利用;烟气中NOx、SO2、烟尘、二噁英、HCl、HF浓度均满足国家标准要求。
4)污泥小比例掺烧在现役机组上应用较广,对机组整体运行影响较小。进一步提高污泥掺烧比例时,仍需注意制粉系统的干燥出力与研磨出力核算,以满足出力裕量要求;同时需监测炉膛烟温变化及管壁结渣情况、污染物排放情况,合理安全地解决市政污泥处置问题。
[1] CHEN H , YAN S H , YE Z L , et al. Utilization of urban sewage sludge: Chinese perspectives[J]. Environmental Science &Pollution Research, 2012,19:1454-1463.
[2] HU M,YE Z H,ZHANG H Y, et al. Thermochemical conversion of sewage sludge for energy and resource recovery:Technical challenges and prospects[J]. Environmental Pollutants and Bioavailability,2021,33(1):145-163.
[3] 环境保护部办公厅.《关于加强城镇污水处理厂污泥污染防治工作的通知》环办[2010]157号[EB/OL].(2010-11-26)[2023-01-31]. https://www.mee.gov.cn/gkml/hbb/bgt/201012/t20101206_198325.htm?keywords=.
[4] 国务院.《国务院关于加强环境保护重点工作的意见》国发[2011]35号[EB/OL].(2011-10-17) [2023-01-31]. https://www.gov.cn/zhengce/content/2011-10/20/content_4672.htm.
[5] 国家发展改革委.《国家发改委关于完善垃圾焚烧发电价格政策的通知》发改价格[2012]801号[EB/OL].(2012-03-28)[2023-01-31]. https://www.gov.cn/zwgk/2012-04/10/content_2109921.htm.
[6] 苏胜,李培生,孙学信,等.污泥基本特性及其与煤混烧的热重研究 [J]. 热力发电,2004,33(9): 69-71,74-85.
SU Sheng,LI Peisheng,SUN Xuexin,et al. Thermogravimetric study on basic characteristic of sewage sludge and its mix building performance with coal [J]. Thermal Power Generation,2004,33(9): 69-71,74-85.
[7] 吕清刚, 范晓旭, 那永洁, 等. 城市下水污泥和煤/LPG 在循环流化床上的混烧试验研究[J]. 工程热物理学报, 2006, 27(2): 339-342.
LYU Qinggang, FAN Xiaoxu, NA Yongjie, et al. Co-combustion of wet sewage sludge and coal/LPG in a pilot scale circulating fluidized bed[J]. Journal of Engineering Thermophysics, 2006, 27(2): 339-342.
[8] 吕清刚, 李志伟, 那永洁, 等. CFBC 混烧城市污泥与煤: N2O 和 NO 的排放[J]. 工程热物理学报, 2004, 25(1): 163-166.
LYU Qinggang, LI Zhiwei, NA Yongjie, et al. N2O and NO emissions from co-firing sewage sludge with coal on CFBC[J]. Journal of Engineering Thermophysics, 2004, 25(1): 163-166.
[9] 田甲蕊. 改性印染污泥干化和掺烧特性研究[D]. 南京: 东南大学, 2015: 38.
[10] 张成,朱天宇,殷立宝,等.100 MW 燃煤锅炉污 泥掺烧试验与数值模拟[J].燃烧科学与技术,2015,21(2):114-123.
ZHANG Cheng,ZHU Tianyu,YIN Libao,et,al.Field test and numerical simulation for co-combustion of sludge in a 100 MW coal fired boiler[J]Journal of Combustion Science and Technology,2015,21(2):114-123.
[11] 朱天宇. 100 MW燃煤锅炉煤粉与污泥混烧数值模拟[D]. 武汉: 华中科技大学, 2015.
[12] 刘永付,王飞,吴奇,等. 大型燃煤电站锅炉协同处置污泥的 试验研究[J]. 能源工程,2013(6): 64-69.
LIU Yongfu,WANG Fei,WU Qi,et al. Experimental study of sludge disposal in a large coal-fired power plant[J]. Energy Engineering,2013(6): 64-69.
[13] 狄万丰,李德波,苗建杰,阙正斌. 燃煤锅炉耦合污泥掺烧现场优化技术研究与应用[C]//中国环境科学学会2022年科学技术年会--环境工程技术创新与应用分会场论文集(四).北京:《环境工程》编辑部,2022:689-694.
[14] 魏林清. 煤粉锅炉污泥掺烧技术的试验研究[J]. 中国资源综合利用, 2008,26(8): 9-12.
WEI Lingqing. Experimental study on mixed burning technology of sludge in pulverized coal boiler[J]. China Resources Comprehensive Utilization, 2008,26(8): 9-12.
[15] 霍小华. 垃圾和污泥共燃过程中重金属的赋存迁移规律[J]. 锅炉技术, 2013, 44(5): 75-78.
HUO Xiaohua. The occurrence and migration mechanism of heavy metal during the co-combustion of municipal solid waste and sludge[J]. Boiler Technology, 2013, 44(5): 75-78.
[16] 武宏香, 赵增立, 何方, 等. 污泥与煤、木屑燃烧过程中重金属排放特性研究[J]. 环境工程学报, 2011, 5(11): 2593-2599.
WU Hongxiang, ZHAO Zengli, HE Fang,et al. Volatility of heavy metals in co-combustion of sludge with coal and wood[J]. Chinese Journal of Environmental Engineering, 2011, 5(11): 2593-2599.
[17] 李建新, 严建华, 池涌, 等. 异重流化床垃圾与煤混烧重金属的排放特性[J]. 中国电机工程学报, 2004, 23(12): 179-183.
LI Jianxin, YAN Jianhua, CHI Yong,et al. Heavy metals emission from a fluidized-bed MSW incinerator[J]. Proceedings of the CSEE, 2004, 23(12): 179-183.
[18] 刘蕴芳, 滕建标, 苏耀明, 等. 煤粉炉掺烧干化污泥的污染物排放研究[J]. 环境工程学报, 2014, 8(11): 4969- 4976.
LIU Yunfang, TENG Jianbiao, SU Yaoming, et al. Research on pollutants emitted from dried sludge blending combustion in coal-powder boiler[J]. Chinese Journal of Environmental Engineering, 2014, 8(11): 4969-4976.
[19] LOPES M H, ABELHA P, LAPA N, et al. The behaviour of ashes and heavy metals during the co-combustion of sewage sludges in a fluidised bed[J]. Waste Management, 2003, 23(9): 859-870.
[20] 单忠健, 叶立贞. 中国煤炭工业百科全书:加工利用·环保卷[M]. 北京:煤炭工业出版社, 1999.
[21] NICOLAS Perrin, RICHARD Dubettier, FREDERICK Lockwood, et al. Oxy combustion for coal power plants: Advantages, solutions and projects[J]. Applied Thermal Engineering, 2015, 74(5):75-82.
[22] 中国煤炭工业协会.煤的燃烧特性测定方法 一维炉法: GB/T 39833—2021[S].北京:国家市场监督管理总局,国家标准化管理委员会,2021.
[23] 西安热工研究院有限公司.煤粉燃烧结渣特性和燃尽率一维火焰测试方法:DL/T1106—2009[S].北京: 中国电力出版社, 2009.
Experiment on the co-burning characteristics of municipal sludge blending with coal(grinding)
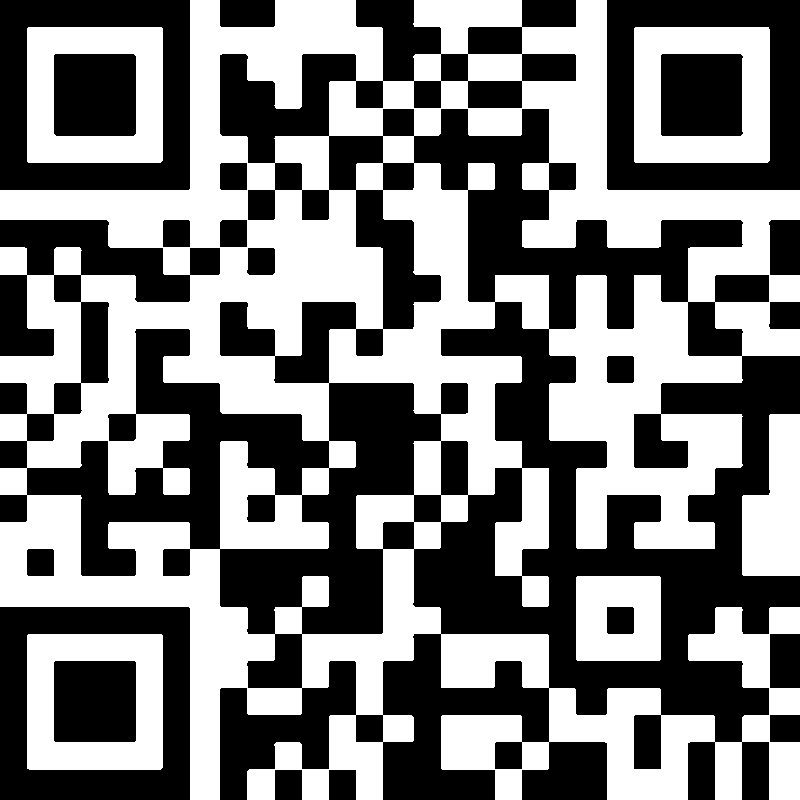
移动阅读
JIA Zixiu,WANG Zhichao,TU Jingyi,et al.Experiment on the co-burning characteristics of municipal sludge blending with coal(grinding)[J].Clean Coal Technology,2023,29(9):51-60.